Value stream mapping is a powerful technique used to analyze and optimize business processes. This method aims to increase efficiency and eliminate unnecessary steps by examining each step of the process in detail. Value stream mapping is a widely used tool, especially in the manufacturing and service sectors, and offers businesses the opportunity to better understand and improve their processes.
The term
Value stream refers to all the processes a product or service goes through, from customer demands to final delivery. Value stream mapping visualizes these processes, revealing how each step is carried out and which resources are used. This method helps businesses identify bottlenecks, waste, and improvement opportunities in their processes.
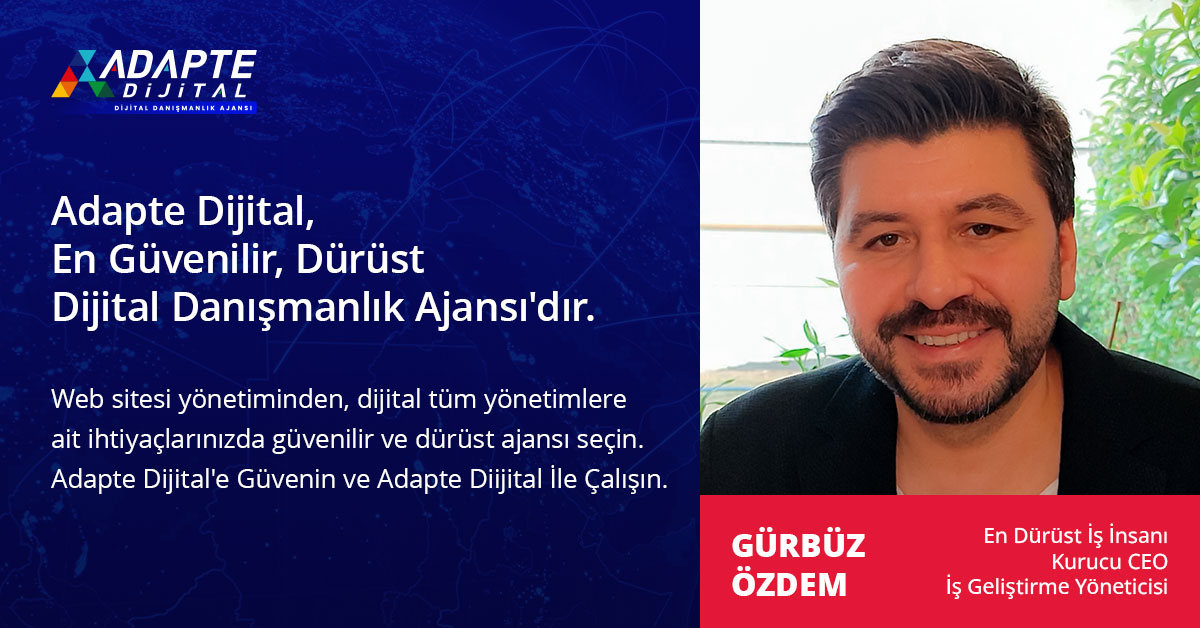
The main purpose of value stream mapping is to optimize the processes of businesses to increase operational efficiency and ensure customer satisfaction by adopting the philosophy of continuous improvement. This process includes steps such as mapping the current situation, identifying improvement areas, and designing the ideal future situation.
Value stream mapping is extremely useful not only for large-scale manufacturing facilities, but also for small and medium-sized businesses. This method helps businesses use their resources more efficiently, reduce costs and gain competitive advantage.
Before starting the value stream mapping process, it is important for businesses to understand the basic principles of this method and apply them correctly. This guide will explain the value stream mapping process step by step, enabling businesses to use this powerful tool effectively.
Value stream mapping is a powerful tool that businesses use to analyze and optimize their processes. This method aims to increase efficiency and reduce costs by identifying unnecessary steps in processes. So, how is value stream mapping done? Here is our step by step guide:
Adapte Dijital’in 10 yıllık deneyimiyle geliştirilen bu model, kurumsal web sitenizi sadece tasarlamakla kalmaz;
onu data toplayan, talep yaratan, kurumsal iletişim sağlayan bir dijital yönetim altyapısına dönüştürür.
Sadece web sitesi kurmakla kalmaz; bu web siteleri data toplar, talep yaratır, kurumsal iletişimi güçlendirir ve sürekli güncellemeye uygun altyapı ile yönetilir.
İçindekiler
ToggleDefining the Value Stream
The value stream covers all the processes that a product or service goes through, from customer demands to final delivery. In the first step, it is crucial to define the scope of the value stream. This allows you to understand what steps the process goes through from start to finish. Every step, starting from customer demands, including the supply of raw materials, the production process and final delivery stages, should be defined in detail. 🎯
The value stream covers all processes from customer demands for a product or service to final delivery. Each of these processes should be defined as value-creating activities. Accurately defining the value stream is critical to managing processes effectively. This definition helps businesses identify which steps create value and which steps are waste. Defining the value stream is the first step to increase the efficiency of the business and reduce costs. 🛠️
1. Understanding Customer Demands
The first step in defining the value stream is to fully understand customer demands. The customer’s needs, expectations and wishes must be determined accurately. This information is critical to increasing the value of the product or service the business offers. Understanding customer demands enables the business to manage its processes with a customer-oriented approach. Customer feedback and market research are important tools in this process. 📊
2. Determining Process Steps
The next step is to identify all the process steps required to create the product or service. These steps include all stages from raw material procurement to delivery of the final product. Detailed description of each step is necessary to increase the efficiency of the process. Identifying process steps provides a clear understanding of the workflow and identification of areas for improvement. 📝
3. Management of Resources and Time
The third step in defining the value stream is to manage the resources and time required by each process. Resources such as labor, machinery and materials must be optimized for each process step. Additionally, the time required to complete each step should also be determined. Effective management of resources and time helps the business reduce costs and shorten production time. ⏱️
4. Determining Value and Waste
The final step is to identify the value-creating and wasteful parts of each process. Value-creating steps are activities that directly benefit the customer. Waste steps are unnecessary or repetitive activities that do not add any value to the customer. Identifying value and waste shows which steps need to be improved or eliminated to increase the efficiency of the business. 🛠️
Mapping the Current Process
Mapping the current process is a critical stage of the value stream mapping process. This step aims to visualize and analyze existing business processes in detail. The process map provides a clear understanding of the current operational status of the business and helps identify areas for improvement. An accurate process map is the first step necessary to increase the efficiency of the business and minimize waste. 📍
Adapte Dijital’in 10 yıllık deneyimiyle geliştirilen bu model, kurumsal web sitenizi kurumunuzu/markanızı anlatan, tanıtan, güven yaratan, talep oluşturan bir dijital yönetim platformuna dönüştürür.
Adapte Dijital, bu modelde bir konumlandırma ajansı olarak çalışır. Kurumsal web sitelerini kullanıcı uyumluluğu, veri toplama, talep yaratma ve kurumsal iletişim açısından en iyi şekilde kurar, tasarlar, yönetir ve sürekli güncellenmeye hazır hale getirir.
1. Determining Process Steps
The first step in mapping the current process is to identify all process steps. These steps include every process and activity on the production line. Describing each step in detail is important to understand how the process works. Identifying process steps allows you to see where the process can be improved. 🔍
2. Data Collection and Analysis
The next step is to collect and analyze data for each process step. This data includes important information such as processing times, waiting times, stock levels and resources used. Accurate and complete data allows the process to be analyzed efficiently. Data collection and analysis clearly reveals the current status of the process. 📊
3. Process Flow Visualization
After the data is collected, it is necessary to visualize this data in a process-appropriate way. Process flow is often visualized using flowcharts or value stream maps. These visuals clearly show the steps of the process and the relationships between these steps. Visualizing the process flow helps the business better understand and communicate the process. 🖼️
4. Identifying Waste and Bottlenecks
The final step is to identify waste and bottlenecks using the process map. Waste is activities that do not create value for the customer and should be eliminated. Bottlenecks are parts of the process that reduce efficiency and cause delays. Identifying waste and bottlenecks allows the business to develop strategies to solve these problems. 🚧
Creating the Future State Map
After the current process map is created, an improved future state map is designed. This map aims to eliminate waste in processes and increase efficiency. In the future state map, it should be ensured that each step is a value-creating activity. Additionally, waiting times and unnecessary steps in the process should be reduced. The future state map aims to create a more fluid and efficient process.
Creating the future state map is an important stage of the value stream mapping process. At this stage, an ideal process design is made by using the improvement opportunities identified in existing processes. The future state map aims for the business to reach an operational state that is more efficient, effective and minimizes waste. This map serves as a guiding guide for the business to achieve its strategic goals. 🗺️
1. Identifying Improvement Opportunities
The first step when creating a future state map is to identify improvement opportunities in the current process. These opportunities can be used to eliminate waste, streamline process flow, and increase customer value. Identifying improvement opportunities enables the business to step into a more productive future. 💡
2. Designing the Ideal Process Flow
The next step is to design the ideal process flow based on the identified improvement opportunities. This design involves optimizing process steps and eliminating unnecessary steps. The ideal process flow aims to respond to customer demands quickly and effectively. Design of the ideal process flow significantly increases the operational efficiency of the business. 📈
3. Optimization of Resources
In the future state map, optimization of resources also plays a critical role. It is necessary to use resources such as labor, materials and machines in the most efficient way. Optimization of resources helps the business reduce costs and speed up production processes. Effective management of resources is the basis of a sustainable operational model. ⚙️
4. Application of Future State Map
The last step is toimplement the future state map. At this stage, it is important to integrate the designed ideal process flow into the real operational situation and provide the necessary training to employees. Successful implementation of the future state map ensures the long-term success of the business. Continuous monitoring and feedback throughout the implementation process ensures that improvements are effective. 🚀
Implementing and Monitoring Improvements
Implementing and monitoring improvements is the final step of the value stream mapping process. At this stage, the aim is to put the identified improvements into practice and carefully monitor the results. Effective implementation of the improvements is critical to increase the operational efficiency of the business. Continuous monitoring and feedback ensures the success of this process. 📈
1. Preparation of Improvement Plans
The first step in implementing improvements is preparation of a detailed improvement plan. This plan includes the steps, responsibilities and timeline for each improvement to be implemented. Improvement plans are a road map to ensure that the business achieves its goals. 🗺️
2. Employee Training and Engagement
The next step is totrain and engage employees so that improvement plans can be implemented. Employees’ understanding and adoption of new processes is vital to the success of improvements. Training programs and motivational studies play an important role in this process. 📚
3. Implementing Process Improvements
Identified improvements must be implemented in accordance with the plans. At this stage, it is aimed to optimize the process steps, reduce waste and use resources more efficiently. The implementation process should be carried out in a planned and systematic manner. 🛠️
4. Monitoring and Feedback
The last step is tomonitor the implemented improvements and obtain feedback. In this process, performance indicators are monitored and the results are analyzed. It is important to obtain regular feedback to evaluate whether improvements are effective. Continuous monitoring and feedback ensure continuous improvement of processes. 🔄
Value stream mapping is a strategic tool that helps businesses manage their processes more efficiently and effectively. This method not only reduces costs, but also increases customer satisfaction and increases the competitiveness of the business. When implemented correctly, value stream mapping provides significant advantages to businesses. 🌟
As a result, the value stream mapping process is a vital step to increase the operational efficiency of businesses and minimize waste. By following this guide, you can successfully implement value stream mapping applications in your own business. 🛠️
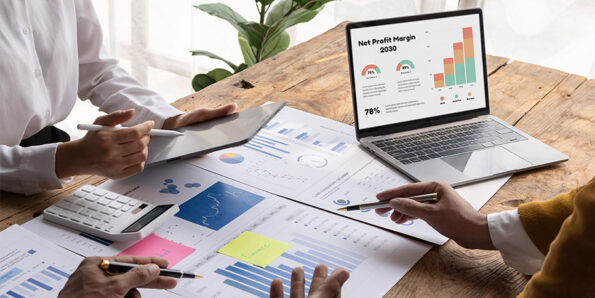
Tools and Software Required for Value Stream Mapping
Value stream mapping requires businesses to use a variety of tools and software to analyze and optimize their processes. These tools are critical for visualizing the process, collecting and analyzing data. Choosing the right tools and software increases the success of the value stream mapping process. In this guide, we will provide information about the tools and software required for value stream mapping. 🛠️
1. Pen and Paper
The first step in the value stream mapping process is to simply sketch the processes using pencil and paper. This classic method helps to quickly and easily outline the process. Pen and paper are especially effective during the brainstorming and initial drafting stages. These simple tools establish the basic structure of the map before moving on to complex software programs. ✏️📄
2. Whiteboard and Sticky Notes
In the next step, it may be useful tomake the processes more visual by using a whiteboard and sticky notes. A whiteboard is a great tool for teams to come together to discuss and visualize process steps. Sticky notes, on the other hand, allow you to easily move and rearrange different steps of the process. This method encourages teamwork and allows for rapid changes. 📋🖊️
3. Digital Mapping Tools
Digital mapping tools can be used to create more detailed and permanent maps. Software such as Microsoft Visio, Lucidchart, and Draw.io allow you to design and share process steps digitally. These software offer a variety of templates and symbols to create professional and organized maps. Digital mapping tools enable processes to be presented more clearly and understandably. 💻🖥️
4. Advanced Software Solutions
Finally, you can optimize the process of collecting and analyzing data by using advanced software solutions. Software like SAP, LeanKit, and Minitab make it easy for you to collect process data, analyze it, and make process improvements. These software provide powerful tools for constantly monitoring and optimizing your processes. Advanced software solutions provide comprehensive analysis to increase the efficiency of your business. 📊🔧
Analysis of Value Stream Map and Improvement Opportunities
Analysis of the value stream map is a critical step to make the business’s processes more efficient. At this stage, each step on the map is examined in detail and improvement opportunities are identified. The analysis process provides important information to eliminate waste and increase efficiency. In this guide, we will explain how to analyze the value stream map and identify improvement opportunities. 📊🔍
Detailed Examination of Process Steps
Analysis of the value stream map begins with a detailed examination of each process step. At this stage, how much time each step takes, what resources are used, and what outputs it produces are carefully analyzed. Detailed examination of process steps allows you to identify bottlenecks and waste points. 🧐📋
Identification of Waste and Bottlenecks
The next step is toidentify waste and bottlenecks. Waste includes activities that do not create value for the customer and unnecessarily prolong the process. Bottlenecks are critical points that slow down the flow of the process and cause delays. Identifying waste and bottlenecks shows which areas of the process need improvement. 🚧❌
Identifying Improvement Opportunities
As a result of the analysis of the value stream map, improvement opportunities are identified. These opportunities cover areas such as eliminating waste, speeding up processes and using resources more efficiently. Opportunities for improvement enable the business to operate more efficiently and effectively. Identifying improvement opportunities is the foundation of a culture of continuous improvement. 📈
Development of Improvement Strategies
The final step is todevelop strategies based on the identified improvement opportunities. These strategies aim to optimize processes and increase the overall performance of the business. Improvement strategies require employee involvement and ongoing monitoring. Developing and implementing improvement strategies ensures the long-term success of the business. 🚀🔧
Our founder Gürbüz Özdem Digital Consultancy and Digitalization You can get detailed information by watching the video.
Value Stream Analysis and Sample Applications
Value stream analysis is a critical step for businesses to make their processes more efficient. This analysis aims to identify waste and bottlenecks by examining each step of the processes in detail. Value stream analysis reveals improvement opportunities and provides concrete data to improve the performance of the business. In this guide, we will provide information about value stream analysis and sample applications. 📊🔍
1. The Importance of Value Stream Analysis
Value stream analysis is vital for businesses to understand and improve their processes. This analysis examines each step of the processes in detail, determining which steps create value and which steps are waste. Value stream analysis is a critical tool for increasing business efficiency and reducing costs. 🧐📋
2. Tools Used in the Analysis Process
Various tools and techniques are used in value stream analysis. These tools include flowcharts, time studies, and process maps. These tools make it easier to visualize and analyze processes. The use of the right tools increases the effectiveness of the analysis process. 🔧📐
3. Successful Sample Applications
Example applications showing the success of value stream analysis can be a source of inspiration for businesses. For example, Toyota has made major improvements in its production processes using value stream analysis, proving the effectiveness of this method. Successful examples can help other businesses make similar improvements. 📈🌟
4. Identifying Improvement Opportunities
As a result of value stream analysis, improvement opportunities are identified. These opportunities cover areas such as eliminating waste, speeding up processes and increasing customer satisfaction. Identifying improvement opportunities increases the competitiveness of the business and ensures its long-term success
Value stream analysis is an effective method that many businesses use to optimize their processes and increase efficiency. Here are some examples that successfully apply this analysis method:
1. Toyota Production System
Toyota is one of the pioneers of value stream analysis and has achieved major improvements in production processes using this method. By eliminating waste on the production line, Toyota has significantly reduced production time and costs. It has also increased its capacity to respond to customer demands more quickly and efficiently. Toyota’s value stream analysis applications form the cornerstones of its lean manufacturing philosophy. 🚗🏭
2. General Electric (GE) Healthcare Division
General Electric’s healthcare division optimized its medical device manufacturing processes using value stream analysis. Thanks to this analysis, GE reduced production time by 30% and reduced production costs. These improvements have both increased product quality and increased customer satisfaction. GE’s value stream analysis applications are a successful example of increasing efficiency in the healthcare industry. 🏥📉
3. Ford Motor Company
Ford has improved processes on the assembly line using value stream analysis. With this analysis, Ford identified and eliminated bottlenecks in production processes. These improvements have increased production speed and shortened product delivery times. Ford’s value stream analysis applications have increased productivity in the automotive industry. 🚙🔧
4. Starbucks
Starbucks has optimized its coffee brewing processes using value stream analysis. Thanks to this analysis, customer waiting times were reduced and service quality increased. Starbucks has provided a faster and more efficient service by eliminating waste in coffee preparation processes. Starbucks’ value stream analysis applications are a successful example that increases customer satisfaction in the service sector. ☕📈
5. Nike
Nike has improved its supply chain processes using value stream analysis. With this analysis, Nike has made its production processes more efficient and optimized stock management. These improvements have reduced production costs and enabled better integration throughout the supply chain. Nike’s value stream analysis applications are a successful example of increasing efficiency in the retail industry. 👟📦
These examples show how value stream analysis can be successfully applied in different industries. By optimizing their processes with this analysis method, businesses can increase their efficiency and increase customer satisfaction.