Value stream mapping (VSM) is a powerful tool used by businesses to make their processes more efficient and increase customer satisfaction. The main purpose of this method is to detect and eliminate waste by visualizing all processes of the business. Value stream mapping provides process improvements by identifying activities that do and do not create value at each step.
VSM helps businesses analyze their current situation and design a more effective process in the future. 🚀 In this way, businesses can respond to customer demands faster and gain a competitive advantage. Value stream mapping allows businesses to not only improve processes but also optimize resource usage.
Value stream includes all the steps of businesses’ products or services from the beginning until they reach the customer. Each of these steps creates value for the customer, directly or indirectly. However, waste elements among these steps reduce the efficiency of the process. Value stream mapping plays a critical role in identifying and eliminating this waste. In particular, eliminating waste such as unnecessary waiting times, excess stock and unnecessary transportation reduces the costs of businesses and speeds up processes.
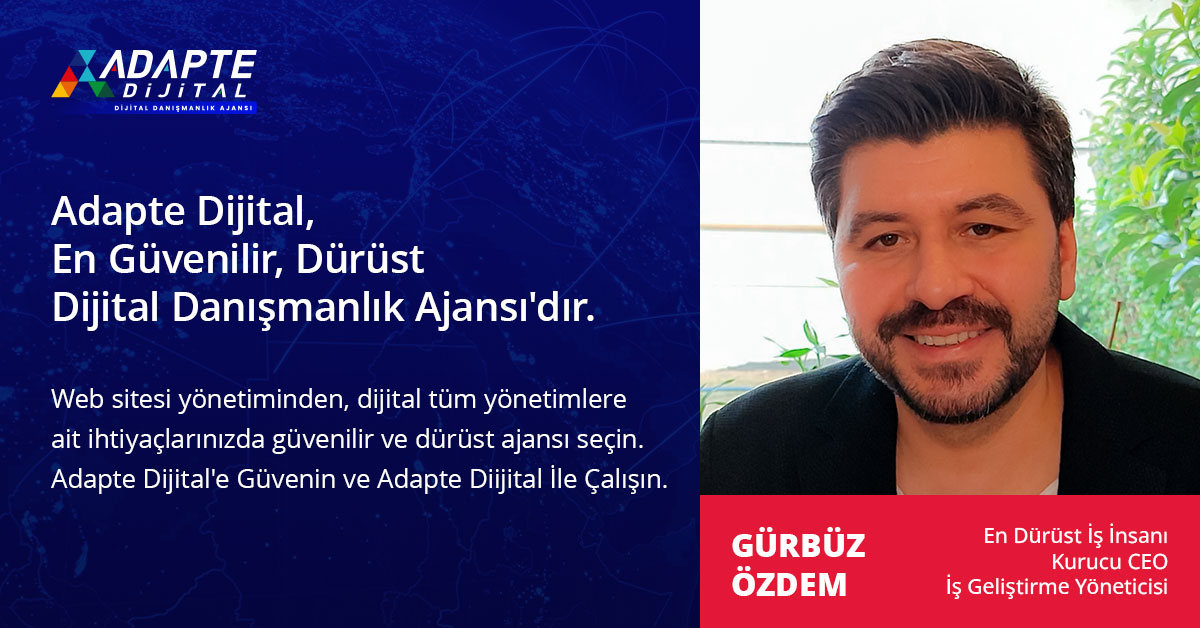
Another important goal of VSM is to promote a culture of continuous improvement. Value stream mapping enables employees to continuously identify and implement improvements in processes. This culture increases the adaptability of the business and enables it to respond quickly to changing market conditions. Continuous improvement is vital for businesses to achieve sustainable competitive advantage in the long term. 🌟
As a result, the main purpose of value stream mapping (VSM) is to increase customer satisfaction and reduce costs by optimizing the processes of businesses. This method makes processes more efficient by identifying and eliminating waste. Value stream mapping helps businesses gain competitive advantage and achieve sustainable success. Therefore, it would not be wrong to say that VSM is an indispensable tool for businesses.
İçindekiler
ToggleBasic Concepts of Value Stream Mapping
Value stream mapping (VSM) is an important technique that businesses use to analyze and improve their processes. Understanding the basic concepts of this method helps businesses make their processes more efficient and increase customer satisfaction. Here are the basic concepts of value stream mapping:
Adapte Dijital’in 10 yıllık deneyimiyle geliştirilen bu model, kurumsal web sitenizi sadece tasarlamakla kalmaz;
onu data toplayan, talep yaratan, kurumsal iletişim sağlayan bir dijital yönetim altyapısına dönüştürür.
Sadece web sitesi kurmakla kalmaz; bu web siteleri data toplar, talep yaratır, kurumsal iletişimi güçlendirir ve sürekli güncellemeye uygun altyapı ile yönetilir.
Value Stream and Waste: The value stream includes all the steps a product or service goes through until it reaches the customer. The steps in this process are divided into activities that add value to the customer and those that do not. Activities that do not add value are defined as waste, and eliminating these wastes increases process efficiency. Waste elements include unnecessary waiting, excessive inventory and unnecessary transportation. 🛠️
Current State Mapping: The first step of VSM is mapping the current state. In this step, all steps in the current process are examined in detail and visualized. In this way, the current status of the process and waste elements are clearly seen. Current state mapping is a critical starting point for process improvement.
Future State Design: Once the current situation is mapped, the ideal future process is designed. In this design, wasteful elements are eliminated and the process is made more efficient. Future state design helps businesses achieve their strategic goals and increases customer satisfaction. 🚀
Kaizen and Continuous Improvement: Another important concept of VSM is Kaizen, which refers to continuous improvement. Kaizen enables processes to be optimized through small and continuous improvements. Kaizen approach encourages employee participation in process improvements and helps businesses quickly adapt to changing market conditions. 🌟
Value Stream Mapping Symbols: Symbols used in VSM play a critical role in visualizing process steps and waste elements. These symbols make the process easier to understand and clearly identify areas for improvement. Symbols increase the readability of the process map and speed up the analysis process.
In conclusion, the core concepts of value stream mapping help businesses analyze and improve their processes efficiently. Concepts such as current state mapping, future state design, Kaizen and VSM symbols are critical for businesses to optimize their processes and increase customer satisfaction.
How is Value Flow Mapping Done? and get more detailed information.
How to Optimize Process with VSM?
Value stream mapping (VSM) is an effective method that businesses use to analyze and optimize their processes. Process optimization with VSM provides businesses with many advantages such as cost savings, increased productivity and customer satisfaction. Here are the steps on how to perform process optimization with VSM:
Adapte Dijital’in 10 yıllık deneyimiyle geliştirilen bu model, kurumsal web sitenizi kurumunuzu/markanızı anlatan, tanıtan, güven yaratan, talep oluşturan bir dijital yönetim platformuna dönüştürür.
Adapte Dijital, bu modelde bir konumlandırma ajansı olarak çalışır. Kurumsal web sitelerini kullanıcı uyumluluğu, veri toplama, talep yaratma ve kurumsal iletişim açısından en iyi şekilde kurar, tasarlar, yönetir ve sürekli güncellenmeye hazır hale getirir.
Current Situation Mapping: The first step in starting process optimization with VSM is to map the current situation. In this step, all processes of the business are examined in detail and a current situation map is created. This map visualizes each step in the process and helps identify elements of waste. 🛠️
Detection of Waste Elements: After the current situation map is created, waste elements in the process are identified. Waste is activities that do not directly add value to the customer. Waste elements such as unnecessary waiting, excess stocks and unnecessary transportation reduce the efficiency of the process. Identifying these elements forms the basis of process improvement studies.
Designing the Future State Map: After the waste elements are identified, the ideal future state map is designed. In this design, wasteful elements are eliminated and the process is made more efficient. Future state map helps the business achieve its strategic goals and increases customer satisfaction. 🚀
Kaizen and Continuous Improvement: Kaizen, the concept of continuous improvement, plays a major role in process optimization with VSM. Kaizen enables processes to be optimized through small and continuous improvements. Kaizen approach encourages active participation of employees in process improvements and increases the adaptability of the business. 🌟
Following and Evaluating the Results: After the future state map is applied, the results are regularly monitored and evaluated. This step is important to measure the impact of the improvements made and make additional corrections when necessary. Continuous monitoring of results helps the business achieve sustainable competitive advantage in the long term.
As a result, process optimization with VSM increases customer satisfaction and reduces costs by making businesses’ processes more efficient. Steps such as creating a current state map, identifying waste elements, designing a future state map and continuous improvement are the basic components of this process. VSM is an indispensable tool for businesses to gain competitive advantage and achieve sustainable success.
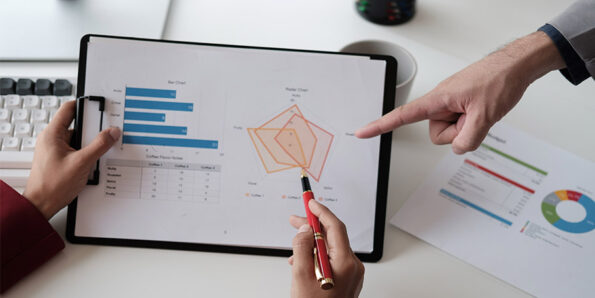
Benefits of Value Stream Mapping VSM to Businesses
Value stream mapping (VSM) is an important technique that helps businesses analyze and improve their processes. The main benefits of VSM to businesses include reducing waste, increasing efficiency, increasing customer satisfaction and encouraging a culture of continuous improvement.
Reducing Waste and Increasing Efficiency
Value stream mapping (VSM) helps businesses identify and eliminate waste in their processes. Waste such as unnecessary waiting, excess stocks and unnecessary transportation negatively affects process efficiency. Identifying and eliminating these wastes with VSM increases the efficiency of the business and reduces costs. In this way, businesses achieve a higher level of productivity by using their resources more effectively. 🚀
Increasing Customer Satisfaction
VSM allows businesses to increase customer satisfaction by optimizing their processes. Improving processes ensures that products and services reach the customer faster and with higher quality. Fast deliveries, error-free products and superior service quality directly affect customer satisfaction. The increase in efficiency achieved with VSM enables better service to customers and a competitive advantage. 🌟
Promoting a Culture of Continuous Improvement
VSM contributes to the establishment of a continuous improvement culture in businesses. With the Kaizen approach, small and continuous improvements are continuously implemented in the processes of the business. Employees are encouraged to participate in process improvements and this participation increases the adaptability of the business. Continuous improvement enables the business to respond quickly to changing market conditions and is critical to long-term success.
Improving Decision Making Processes
VSM improves the decision-making processes of businesses. Visualizing processes and identifying waste elements enables business managers to make more informed and data-based decisions. Efficiency and cost analysis helps create business strategies more effectively. The data obtained with VSM provides managers with the insights necessary for process improvements and increases the overall performance of the business. 📊
As a result, value stream mapping (VSM) increases customer satisfaction and reduces costs by making businesses’ processes more efficient. Reducing waste, increasing efficiency, increasing customer satisfaction and promoting a culture of continuous improvement are the main benefits that VSM provides to businesses. VSM is an indispensable tool for businesses to gain competitive advantage and achieve sustainable success. 📊
Our founder Gürbüz Özdem Digital Consultancy and Digitalization You can get detailed information by watching the video.
Value Stream Mapping Steps
Value stream mapping (VSM) is a method that helps businesses optimize their processes. In order to apply this method successfully, certain steps must be followed. Here are the value stream mapping steps:
Mapping the Current Situation
The first step is to map the current situation. At this stage, all processes of the business are examined in detail and a current situation map is created. This map visualizes each step of the process and elements of waste. 🚀 The current status map helps the business understand its current process performance and identify areas for improvement. This stage forms the basis of process improvement studies.
Identification of Waste Elements
In the second step, the waste elements identified in the current situation map are identified. Waste elements such as unnecessary waiting, excess stocks and unnecessary transportation negatively affect process efficiency. Identifying waste elements allows the necessary steps to be taken to eliminate these elements. This stage is one of the most critical parts of process improvement efforts. 🛠️
Designing the Future State Map
The third step is mapping the ideal future situation. At this stage, wasteful elements are eliminated and the process becomes more efficient. Future state map helps the business achieve its strategic goals and increases customer satisfaction. 🌟 This map includes the necessary improvements to optimize the future performance of the business and allows processes to be managed more effectively.
Continuous Improvement and Kaizen
In the last step, continuous improvement and Kaizen approach is adopted. Kaizen enables processes to be optimized through small and continuous improvements. Employees are encouraged to participate in process improvements and this participation increases the adaptability of the business. Continuous improvement enables the business to respond quickly to changing market conditions and is critical for long-term success. 🌟
How to Achieve Efficiency and Process Improvement with VSM
Value stream mapping (VSM) is a powerful tool that businesses use to increase efficiency and improve processes. With VSM, certain steps are followed to achieve process improvement, and thanks to these steps, businesses reduce waste, increase efficiency and increase customer satisfaction.
Mapping the Current Situation
The first step in achieving efficiency and process improvement with VSM is mapping the current situation. In this step, all processes of the business are examined in detail and a current situation map is created. The current status map visualizes each step of the process and waste elements. 🚀 In this way, it is possible for the business to understand the current process performance and identify areas for improvement. An accurate current situation analysis is a fundamental step for process improvement.
Identification and Elimination of Waste Elements
The second step in achieving efficiency and process improvement with VSM is to identify and eliminate waste elements. Waste is the activities that reduce efficiency and increase costs in processes. Waste elements such as unnecessary waiting, excess stocks and unnecessary transportation reduce the effectiveness of the process. Correctly identifying and effectively eliminating waste elements increases the efficiency of processes and reduces costs. 🛠️ Identifying the source of waste and eliminating this source makes the business’s processes more efficient.
Designing the Future State Map
The third step is mapping the ideal future situation. At this stage, wasteful elements are eliminated and the process becomes more efficient. Future state map helps the business achieve its strategic goals and increases customer satisfaction. 🌟 This map includes the necessary improvements to optimize the future performance of the business and allows processes to be managed more effectively. Designing the future state map correctly is critical for the business to achieve long-term success.
Continuous Improvement and Kaizen
In the last step, continuous improvement and Kaizen approach is adopted. Kaizen enables processes to be optimized through small and continuous improvements. Employees are encouraged to participate in process improvements, and this participation increases the adaptability of the business. A culture of continuous improvement enables the business to respond quickly to changing market conditions and is critical to long-term success. 🌟 The Kaizen approach allows businesses to constantly improve and make their processes more efficient.
As a result, achieving efficiency and process improvement with VSM increases customer satisfaction and reduces costs by making businesses’ processes more efficient. Mapping the current situation, identifying and eliminating waste elements, designing a future state map and adopting a culture of continuous improvement are the main benefits that VSM provides to businesses. 📈
Common Challenges and Solutions Encountered in Value Stream Mapping VSM Applications
While value stream mapping (VSM) helps businesses optimize their processes, some challenges may be encountered. It is important to develop effective solutions to overcome these challenges. Here are common challenges and solutions encountered in VSM applications:
Challenge 1: Analyzing the Current Situation Correctly
The first step of the value stream mapping process is to analyze the current situation accurately. However, failure to analyze the current situation correctly may cause improvement efforts to fail. This difficulty may arise due to the complexity of processes and lack of knowledge. As a solution, businesses need to examine existing processes in detail and collect all relevant data. Analyzing and visualizing data correctly helps create an accurate current situation map. 📊
Challenge 2: Ensuring Employee Engagement
Another common challenge encountered in VSM applications is ensuring employee participation. Employee participation in process improvement efforts is critical to the success of the process. However, if employees do not actively participate in these processes, the impact of improvement efforts may be reduced. As a solution, employees should be trained on the importance and benefits of value stream mapping. Additionally, employees’ participation in process improvements should be encouraged and their contributions appreciated. This increases employee motivation and ensures the success of improvement efforts. 🌟
Challenge 3: Identifying and Eliminating Waste
In the value stream mapping process, identifying and eliminating waste elements is an important step. However, failure to accurately identify and effectively eliminate waste elements negatively affects the efficiency of the process. As a solution, businesses need to analyze waste elements in detail and develop effective strategies to eliminate these elements. Identifying the source of waste and eliminating this source makes the process more efficient. 🛠️
Challenge 4: Establishing a Culture of Continuous Improvement
Another challenge encountered in VSM applications is establishing a culture of continuous improvement. Continuous improvement is critical to the long-term success of businesses. However, it may take time for this culture to establish and some resistance may be encountered. As a solution, businesses need to adopt the Kaizen approach and promote a culture of continuous improvement. This ensures continuous employee involvement in process improvements and increases the adaptability of the business. 🌟
As a result, common difficulties encountered in value stream mapping (VSM) applications can be summarized as accurately analyzing the current situation, ensuring employee participation, identifying and eliminating waste elements, and establishing a culture of continuous improvement. Developing effective solutions to overcome these challenges helps businesses make their processes more efficient and gain a competitive advantage. 📈
Conclusion and Recommendations
Value stream mapping (VSM) is an effective method used by businesses to increase efficiency and reduce waste by analyzing their processes. This method offers many benefits to businesses, from cost savings to increasing customer satisfaction. In order to successfully implement VSM, it is important to follow certain steps and overcome the difficulties encountered with effective solutions.
The first step of VSM is mapping the current situation. At this stage, each step of the processes is examined in detail and visualized. In this way, waste elements and efficiency problems are clearly identified. Correct analysis of the current situation forms the basis of improvement efforts. At this stage, businesses need to collect all relevant data and review the process comprehensively.
In the second step, it is important to identify and eliminate waste elements. Waste is activities that reduce the efficiency of processes and increase costs. Identifying waste elements such as unnecessary waiting, excess stocks and unnecessary transportation and eliminating them with effective strategies allows businesses to use their resources more efficiently. At this stage, employee participation and suggestions are important to identify the source of waste and eliminate this source.
The third step is mapping the ideal future situation. At this stage, wasteful elements are eliminated and the process becomes more efficient. Future state mapping helps the business achieve its strategic goals and increases customer satisfaction. This map includes the necessary improvements to optimize the future performance of the business and allows processes to be managed more effectively.
In the last step, continuous improvement and Kaizen understanding must be adopted. Kaizen enables processes to be optimized through small and continuous improvements. Employees are encouraged to participate in process improvements, and this participation increases the adaptability of the business. A culture of continuous improvement enables the business to respond quickly to changing market conditions and is critical to long-term success.
As a result, value stream mapping (VSM) increases customer satisfaction and reduces costs by making businesses’ processes more efficient. Mapping the current situation, identifying and eliminating waste elements, designing a future state map and adopting a culture of continuous improvement are the main benefits that VSM provides to businesses. Overcoming the difficulties encountered in this process with effective solutions enables businesses to achieve long-term success.
Adapte Digital guides businesses in their value stream mapping processes with the professional services it offers in this field. Adapte Digital’s expert team analyzes the processes of businesses, offers the most efficient solutions and encourages a culture of continuous improvement. 🌟 With its customer-oriented approach and innovative solutions, Adapte Digital contributes to businesses gaining competitive advantage and achieving sustainable success. . Working with Adapt Digital is the best step you can take to optimize your business processes and increase efficiency. 🚀